How are Cigars Made: From Farm to Table
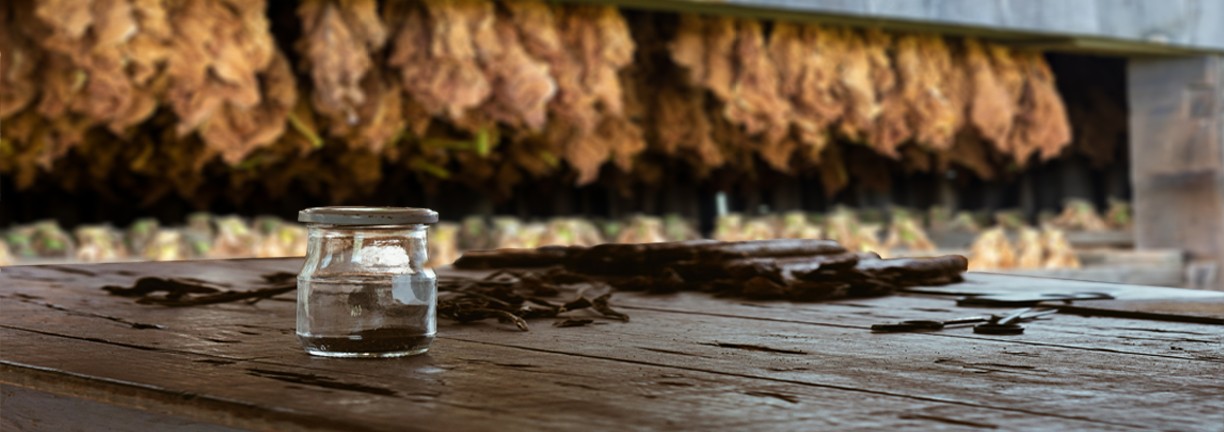
Have you ever wondered about the fascinating process behind the making of cigars? From the fields where the tobacco is grown to the hands of skilled artisans who roll them, the journey of a cigar is a truly intricate and labor-intensive one.
The journey begins in the vast tobacco fields, where the seeds of the Nicotiana tabacum plant are sown with care and patience. Over several months, these tiny seeds sprout into sturdy plants, their broad leaves soaking up the sun's rays and absorbing nutrients from the fertile soil. As the plants mature, skilled farmers diligently tend to them, ensuring optimal growing conditions and guarding against pests and diseases.
Once the tobacco leaves reach their peak ripeness, they are carefully harvested by hand, one by one, to avoid damaging the delicate leaves. This labor-intensive process requires precision and expertise to select only the finest leaves for cigar production. The leaves are then sorted based on their size, texture, and strength, laying the foundation for the diverse flavors and aromas that will characterize each cigar.
Next, the selected leaves undergo a meticulous curing and fermentation process, where they are carefully stacked and aged in temperature-controlled barns. This crucial step allows the leaves to develop complex flavors and aromas while mellowing out any harshness or bitterness. Skilled artisans known as torcedores then take over, expertly rolling the fermented leaves into cigars of various shapes and sizes, each one a testament to centuries-old traditions and craftsmanship.
From start to finish, the journey of a cigar is a labor of love, requiring patience, skill, and dedication at every stage. And as each cigar makes its way from the fields to the hands of aficionados around the world, it carries with it the rich history and legacy of this timeless art form. Now lets look at each process in detail…
Cultivation and Harvesting of Tobacco
Tobacco, one of the most widely cultivated and harvested crops in the world, holds a long-standing history and significance in various cultures. Used for both recreational and ceremonial purposes, its cultivation and harvesting process have evolved over the centuries to meet the demand for this highly-valued commodity.
The cultivation of tobacco typically begins in well-prepared fields where the ideal climate and soil conditions are met. This crop requires warm temperatures, ample sunlight, and a well-drained soil rich in nutrients. To ensure optimal conditions, farmers often choose locations with a moderate climate and fertile land. Additionally, the soil is routinely tested and amended to maintain the necessary balance of pH and nutrients.
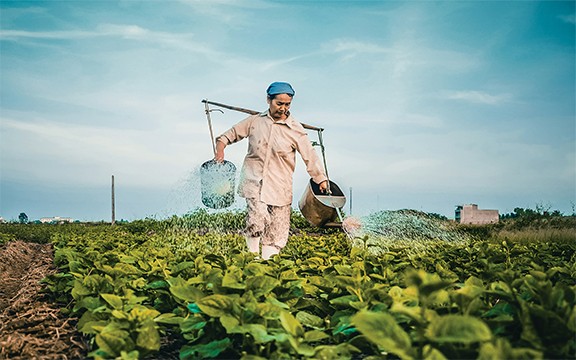
The tobacco plant is usually grown from seeds, which are sowed in specially designated seedbeds. These beds are maintained at a controlled temperature and humidity until the seeds germinate. Once sprouted, the seedlings are carefully transplanted to the fields, allowing them ample space to grow and flourish.
As the tobacco plants mature, they require consistent care and attention. Farmers monitor their growth, regularly watering and fertilizing the plants to promote health and vitality. To prevent the accumulation of pests and diseases, diligent pest management strategies are implemented, including the use of insecticides and fungicides when necessary.
Harvesting tobacco is a labor-intensive process that requires precision and timing. Determining the right moment to harvest the crop is crucial, as it impacts the flavor, aroma, and quality of the tobacco leaves. Typically, the leaves are harvested when they reach their peak ripeness, just before they start to deteriorate. This often involves removing the individual leaves from the bottom of the plant upwards, allowing the upper leaves to continue to mature.
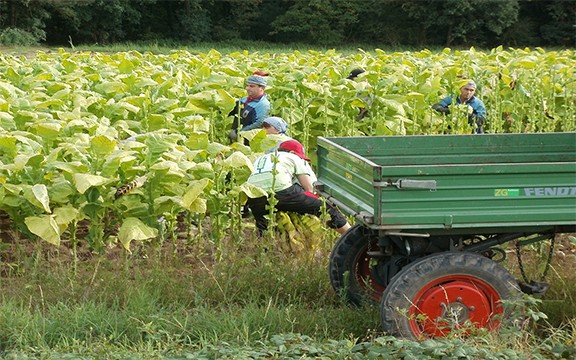
Once harvested, the tobacco leaves undergo curing, a drying process that removes moisture and enhances their flavor. Traditionally, curing was done by hanging the leaves in barns or curing sheds, where they would slowly air dry over several weeks. Nowadays, modern techniques such as flue curing, fire curing, and sun-curing are also used to expedite the process while maintaining the desired characteristics of the tobacco.
After curing, the tobacco leaves are graded and sorted according to their size, texture, and quality. Skilled workers meticulously evaluate each leaf to determine its suitability for different tobacco products, such as cigarettes, cigars, or pipe tobacco. The leaves are then packed and transported to tobacco manufacturing facilities where they undergo further processing and blending to create various tobacco products.
Curing and Fermentation Process
Following the meticulous process of cultivation and harvesting, tobacco leaves undergo a crucial stage known as curing and fermentation. This transformative process is essential for developing the distinctive flavors and aromas that characterize different types of tobacco products, including cigars, cigarettes, and pipe tobacco.
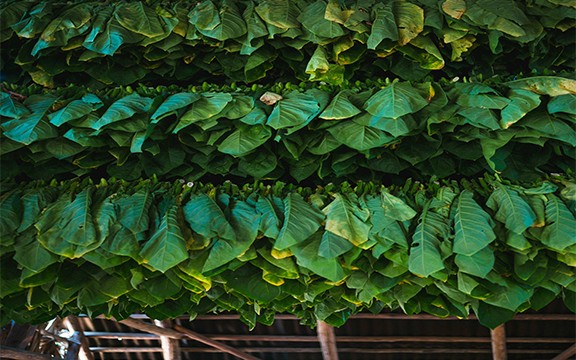
Curing begins shortly after the tobacco leaves are harvested, aiming to remove excess moisture while preserving their natural properties. Traditionally, curing involved hanging the leaves in barns or curing sheds, where they would gradually air dry over several weeks. This method allowed the leaves to slowly develop their flavors and aromas while maintaining their integrity.
In modern times, various techniques have been developed to expedite the curing process while preserving the desired characteristics of the tobacco. Flue curing, for example, involves passing heated air through enclosed chambers where the tobacco leaves are hung, accelerating the drying process. Fire curing, on the other hand, utilizes open fires to generate smoke that imparts unique smoky flavors to the tobacco leaves. Additionally, sun-curing involves exposing the leaves to direct sunlight, allowing them to dry naturally while absorbing the sun's warmth.
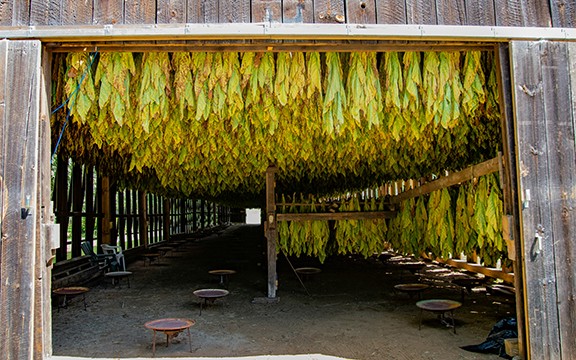
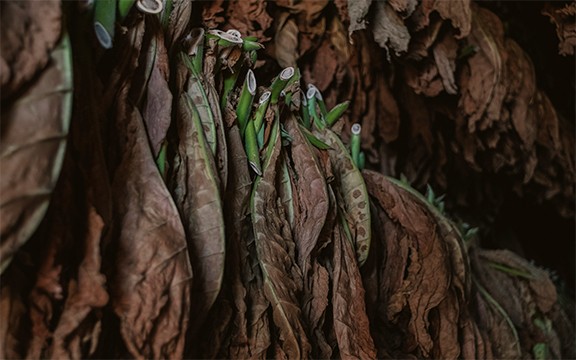
Regardless of the curing method employed, the next crucial step is fermentation. During fermentation, the cured tobacco leaves are stacked in large piles, known as pilons, where they undergo a controlled decomposition process. This fermentation process allows the leaves to further develop their flavors and aromas while reducing bitterness and acidity. Skilled workers carefully monitor the temperature and moisture levels within the pilons, periodically turning the leaves to ensure even fermentation.
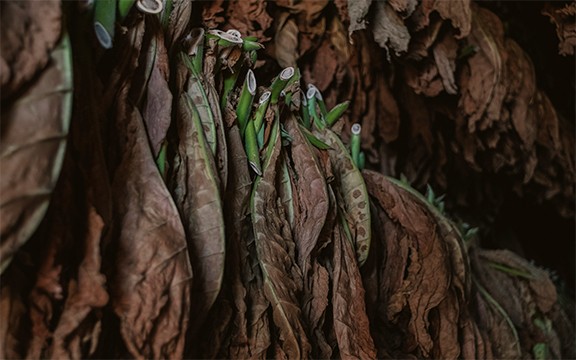
The duration of fermentation can vary depending on the desired characteristics of the final product. Some tobaccos may undergo fermentation for several months or even years to achieve the desired flavor profile. Throughout the fermentation process, the tobacco leaves undergo chemical changes, breaking down complex compounds and releasing volatile compounds that contribute to the overall flavor and aroma.
Once fermentation is complete, the tobacco leaves are graded and sorted based on their quality and characteristics. They are then ready to be blended with other tobaccos and processed into various tobacco products, each reflecting the unique journey of cultivation, harvesting, curing, and fermentation that transforms raw tobacco leaves into cherished smoking experiences.
Sorting and Aging of Tobacco Leaves
Sorting of tobacco leaves is an important step in the production cycle, which involves separating the leaves according to their grade, size, color, and moisture content. This meticulous process ensures that only the finest leaves with desirable characteristics are used for premium tobacco products. During sorting, experienced professionals carefully inspect and judge each leaf, classifying them based on their quality.
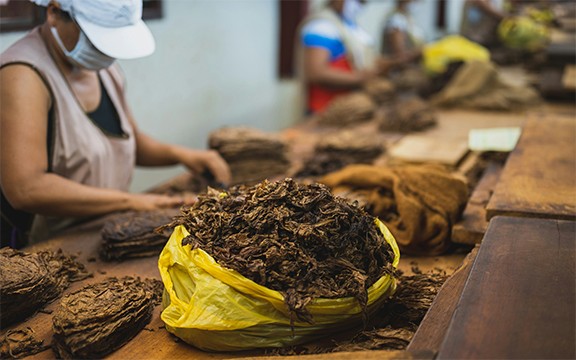
Leaf grade is a crucial aspect of tobacco sorting. Leaves are graded based on their size, appearance, and texture. Typically, tobacco leaves can be categorized into various grades, such as wrapper, binder, filler, and cut filler. Wrapper leaves are of the highest quality, visually appealing, and used to cover the outside of cigars, while binder leaves are used to hold the tobacco blend together. Filler leaves, which form the core of cigars or are used in cigarette manufacturing, vary in grade depending on their size and texture. Cut filler leaves, as the name suggests, are smaller, chopped pieces used in pipe tobacco or as a filler in cigarettes.
Besides sorting, aging is another critical process that greatly impacts the taste and overall quality of tobacco products. After sorting, tobacco leaves are carefully stored and aged for a specific duration to develop their flavors and reduce harshness. Aging allows the leaves to undergo a process called fermenting, where chemical reactions occur, leading to changes in aroma, color, and taste. During this natural transformation, certain undesirable compounds like moisture, tannins, and nicotine levels decrease, resulting in a smoother and more refined product.
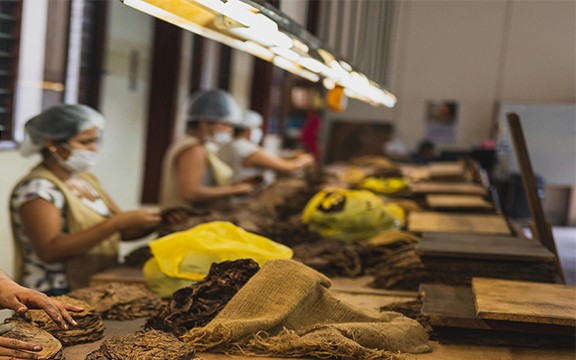
The duration of aging varies depending on the type of tobacco being produced and the desired flavor profile. Generally, the longer the aging process, the more complex and nuanced the taste and aroma. For example, premium cigars often undergo an aging period of several months or even years, whereas cigarette tobacco may have a shorter aging period.
Aging is primarily done under controlled conditions, including temperature and humidity, to maintain consistency and prevent spoilage. Traditionally, tobacco leaves were aged in large wooden barrels or casings known as hogsheads. Nowadays, modern facilities use specially designed rooms equipped with precise climate control systems to create the optimal aging environment.
Crafting the Filler, Binder, and Wrapper
Ask any cigar aficionado, and they will tell you that a good cigar is an art form, meticulously crafted to provide an unforgettable smoking experience. Beyond the rich flavors and aromas, the key components that contribute to a fine cigar are the filler, binder, and wrapper. These elements work together harmoniously, showcasing the skills and expertise of the cigar maker.
The filler, often considered the heart of a cigar, is responsible for delivering the distinctive blend of flavors and aromas that make each cigar unique. Typically, it consists of a blend of whole tobacco leaves, carefully chosen to create a balanced and complex taste profile. Master blenders spend years honing their skills, selecting tobacco leaves from different regions and aging them to perfection. Depending on the desired strength and flavor, the filler leaves may include a combination of ligero, seco, and volado leaves, each contributing its own character to the final product.
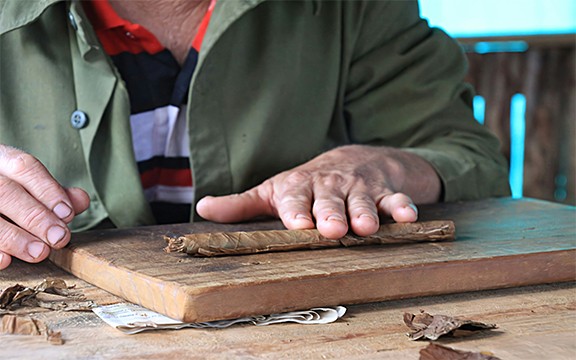
The binder, on the other hand, is the glue that holds the filler leaves together. Made from a durable tobacco leaf, it is essential in ensuring the structural integrity of the cigar. A good binder provides an even burn and prevents the filler leaves from unraveling during smoking. It requires precision and skill to properly wrap and secure the filler, as any loose binding can compromise the overall smoking experience. Experienced cigar makers often use special techniques, such as the entubado method, to ensure the binder tightly encases the filler, allowing for an optimal draw and burn rate.
Lastly, the wrapper serves as the outermost layer of the cigar, adding the finishing touch to its appearance and influencing its flavor. The wrapper leaf is carefully chosen for its texture, aroma, and color. A darker wrapper, such as a Maduro leaf, may provide a richer and sweeter flavor, while a lighter shade, like a Connecticut shade leaf, tends to deliver a milder taste. The wrapper is meticulously applied, with special attention given to the cigar's construction and appearance. It should be smooth, flexible, and free from blemishes or imperfections. Experienced hands skillfully manipulate the wrapper leaf, ensuring a seamless and tight bond around the cigar, allowing for an even burn and enhancing the overall smoking experience.
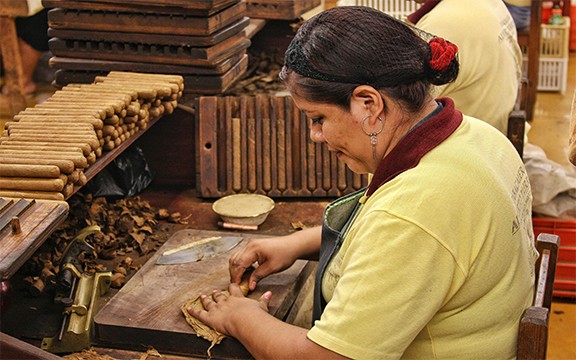
Crafting the filler, binder, and wrapper is a labor-intensive process that demands patience, precision, and expertise. It is a true testament to the passion and commitment of the cigar maker, as they strive for perfection in every aspect of cigar construction. Each element must be meticulously selected and expertly handled, resulting in a symphony of flavors and aromas that tantalize the senses of cigar enthusiasts around the world.
So, the next time you hold a fine cigar in your hand, take a moment to appreciate the craftsmanship behind its creation. From the carefully selected filler leaves to the skillfully applied binder and wrapper, each component plays a crucial role in the delightful journey that awaits when you light up and savor the artistry within.
Role of the Torcedor: Hand-Rolling Cigars
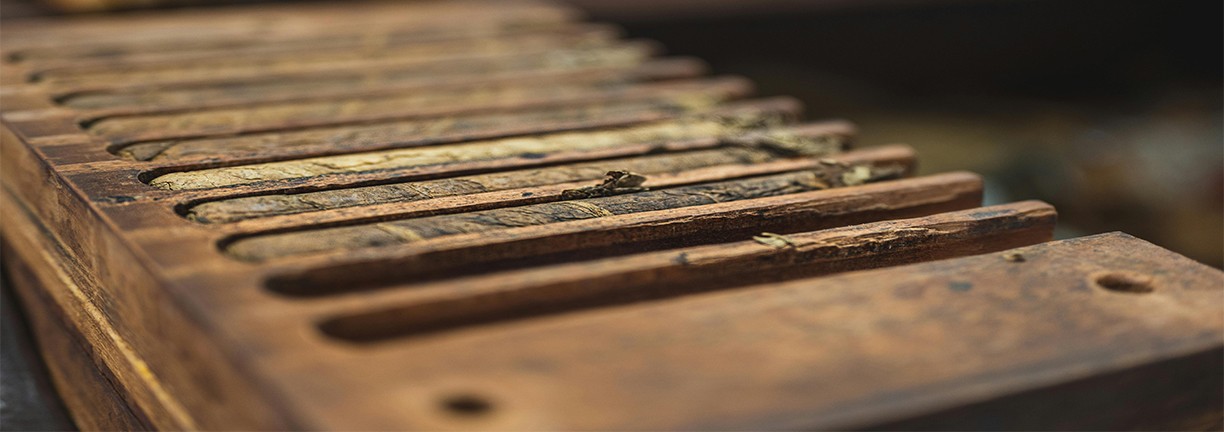
Cigar smoking is an art form that has been perfected over centuries. From the agricultural cultivation of high-quality tobacco leaves to the careful blending and aging process, every step along the way contributes to the final product. One of the most important and mesmerizing stages in the creation of a cigar is the hand-rolling process, or as it's known in Spanish, "torcer."
The torcedor, also known as a cigar roller, is a highly skilled artisan who transforms dried tobacco leaves into masterpieces of craftsmanship. These talented individuals have a deep understanding of the tobacco leaves, their unique characteristics, and how to manipulate them to create the desired flavor, aroma, and burning qualities.
The torcedores work in cigar factories, typically in regions with a rich tobacco-growing tradition, such as Cuba, the Dominican Republic, Nicaragua, and Honduras. They often spend years perfecting their craft and undergo extensive training to become masters of the art of hand-rolling cigars.
The process of rolling a cigar starts with selecting the appropriate tobacco leaves. The torcedor will carefully examine each leaf, assessing its quality, texture, and color. Different leaves serve different purposes in a cigar, such as providing the filler, binder, or wrapper. The torcedor must possess an exceptional knowledge of tobacco blending to ensure a well-balanced and flavorful smoking experience.
Once the leaves have been selected, the torcedor moves on to the rolling stage. This is a delicate process that requires precision and finesse. The torcedor skillfully lays the filler leaves in the desired pattern, ensuring an even distribution of flavors and perfect draw once the cigar is lit. They then wrap the binder leaf around the filler, creating the body of the cigar.
The final step is the application of the wrapper leaf, which gives the cigar its attractive appearance and smooth texture. The torcedor gently places the leaf around the body of the cigar, utilizing their expert touch to maintain the cigar's shape and avoid any rips or tears. They skillfully seal the end with a dab of vegetable gum, the "cap," which is later cut by the smoker before lighting.
The torcedor's role goes beyond mere construction; they also contribute to the overall quality of the cigar. By paying attention to details like the density of the pack and the shape of the cigar, they ensure a consistent and pleasurable smoking experience. A well-rolled cigar will burn evenly, maintain a steady temperature, and release complex flavors and aromas.
The craftsmanship of a torcedor is revered by cigar aficionados worldwide. Their work highlights the artistry and dedication that goes into a hand-rolled cigar, making each puff a unique sensory experience. Their skilled hands and deep knowledge of tobacco enable them to create cigars that capture the essence of the land where the leaves were grown.
Next time you hold a hand-rolled cigar, take a moment to appreciate the torcedor's contribution to your smoking pleasure. Their role as the architect of your smoke should not be underestimated. Hand-rolling cigars is more than just a job; it's a passion and an honored tradition that adds an extra layer of magic to the world of cigars.
Check out out premium cigar cutter!
Quality Control and Inspection
Quality control and inspection are not just technical processes; they're a labor of love, a dedication to craftsmanship, and a commitment to excellence. Every step of the way, from the careful selection of tobacco leaves to the final packaging of the cigars, skilled artisans pour their expertise and passion into ensuring that each cigar meets the highest standards.
Imagine the scene in a cigar factory: rows of seasoned torcedores delicately rolling each cigar by hand, their practiced fingers moving with precision and care. Supervisors walk among them, their watchful eyes trained on the quality of each cigar taking shape. It's not just about meeting quotas or deadlines; it's about honoring a tradition that spans generations and delivering a product that reflects the pride of the craftsmen behind it.
Once rolled, the cigars undergo a thorough inspection. Every detail is scrutinized, from the smoothness of the wrapper to the firmness of the pack. Inspectors run their fingers over each cigar, feeling for imperfections that could affect the smoking experience. They know that even the smallest flaw can detract from the enjoyment of a fine cigar, so they leave no leaf unturned in their quest for perfection.
But quality control doesn't stop at the visual inspection. Cigars are also subject to sensory evaluation, where experienced tasters sample each batch to assess its flavor, aroma, and smoking characteristics. It's a process that requires both expertise and intuition, as they draw on their years of experience to discern subtle nuances in taste and aroma.
Throughout it all, there's a sense of pride and camaraderie among the workers. They know that they're not just making cigars; they're upholding a tradition, preserving a craft, and creating a product that brings joy to connoisseurs around the world. And when a batch of cigars passes inspection and is deemed ready for market, there's a collective sense of satisfaction knowing that they've done their part to ensure that every cigar that bears their company's name is nothing short of exceptional.
Modern Innovations in Cigar Manufacturing
In the world of luxury indulgences, cigars hold a special place. Appreciated by connoisseurs for their intricate flavors and aromas, cigars are a symbol of sophistication and relaxation. Over the years, the art of cigar manufacturing has evolved tremendously, embracing modern innovations to meet the ever-changing demands of discerning smokers.
-
Improvement in Cultivation and Fermentation Techniques
One significant innovation in cigar manufacturing is the improvement in tobacco cultivation and fermentation techniques. Today, farmers have access to cutting-edge farming practices and technology that enables them to produce superior quality tobacco leaves. From precise irrigation systems to climate-controlled barns, every element is carefully managed to cultivate the finest tobacco leaves with a balance of strength and flavor.
-
Development of Hybrid Tobacco Seeds
Another groundbreaking innovation is the development of hybrid tobacco seeds. Through meticulous crossbreeding, tobacco experts have created hybrid varieties that possess desirable traits such as disease resistance, enhanced flavors, and increased yields. These improved seeds ensure consistency in the quality of tobacco, leading to a more enjoyable smoking experience for enthusiasts.
-
Improvement in Blending and Aging Process
Moreover, the blending and aging processes have seen remarkable advancements. Traditionally, blenders carefully selected leaves from different regions to achieve a specific flavor profile. Today, aided by technology, blenders can simulate and analyze countless combinations of tobacco leaves to create unique blends. This allows for a greater range of flavors and complexities, catering to the diverse preferences of cigar enthusiasts.
Aging, a crucial step in cigar production, has also benefitted from modern innovations. Traditionally, cigars were aged in large wooden barrels for months or even years. Now, with the introduction of microclimate aging rooms, manufacturers can emulate the conditions found in a barrel but on a smaller, more controlled scale. This technique allows for faster and more precise aging, resulting in a smoother and more refined smoking experience.
Lastly, packaging and preservation techniques have seen significant innovations. To protect cigars from drying out or losing their freshness, manufacturers have introduced advanced humidification systems. These systems are capable of maintaining precise levels of humidity, guaranteeing that each cigar arrives in perfect condition to the customer. Additionally, packaging has become more robust and visually appealing, using materials that not only safeguard the cigars but also add to their overall aesthetic appeal.
Conclusion
In a world of ever-evolving trends and fads, there are some traditions that remain steadfast, holding on to their timeless charm and appeal. One such tradition is the art of cigar making, an age-old practice that continues to captivate connoisseurs and enthusiasts alike.
The act of crafting cigars is a meticulous process that combines skill, knowledge, and dedication. It is an art form that has been passed down through generations, embodying the essence of craftsmanship and the preservation of history.
Cigar making begins with the selection and blending of tobacco leaves. Each leaf is carefully chosen for its flavor, strength, and aroma, creating the foundation of a memorable cigar. Master blenders spend years honing their senses, acquiring an intimate understanding of the different tobacco varieties and their characteristics.
Once the leaves have been chosen, they are skillfully rolled by hand into a cigar shape. This delicate step requires precision and finesse, as the roller must ensure an even distribution of the tobacco and a tightly wrapped construction. This process is often performed by highly skilled craftsmen, who have dedicated their lives to perfecting the art of rolling cigars.
After the cigars are rolled, they are left to age in a temperature and humidity-controlled environment. This aging process allows the flavors to meld and develop, resulting in a refined and well-balanced smoking experience. The patience required in waiting for the cigars to reach their peak maturity is a testament to the dedication of those involved in the cigar-making industry.
Cigar making is not merely a production process; it is a celebration of culture, heritage, and history. The art of crafting cigars holds a profound significance in many regions around the world, serving as a symbol of prestige and elegance. From the tobacco fields of Cuba to the cigar factories of Nicaragua, each country has its own unique approach to cigar making, giving rise to a wide array of distinct flavors and styles.
Beyond the craftsmanship, smoking cigars is an experience that has been woven into social traditions, providing a moment of relaxation and camaraderie. For many, it is a way to retreat from the fast-paced world, indulging in a ritual of contemplation and enjoyment. The act of lighting and relishing a hand-rolled cigar has become synonymous with sophistication and refinement.
As we reflect on the art and tradition of cigar making, it becomes evident that there is something truly special about this centuries-old practice. The meticulous attention to detail, the passion for quality, and the reverence for the past all contribute to the allure of cigars. While the world around us continues to change, the culture of cigar making remains an unwavering reminder of the beauty found in traditions that stand the test of time.
Article you might be interested in
How to Cut a Cigar Without a Cutter?
A Beginner's Guide to Different Types of Cigars
Cigar vs Cigarette: Understanding the Key Differences
Cigar Punch vs Cutter: Which Tool Will Enhance Your Cigar Smoking Experience?
📍 Based in the USA
📦 Fast Shipping | 💳 Secure Checkout | ❤️ Loved by Thousands
Need help with your order?
📧 support@bargzny.com
Customer service hours: Mon–Fri, 9AM–5PM EST
© 2025 Bargz Oils. All rights reserved www.Bargzny.com